Review of single and multi-degree of freedom (mdof) systems: MTS Tuned MASS Damper Systems
The purpose of a Tuned Mass Damper is to reduce wind excited periodic motion by increasing the apparent damping of structures with low inherent damping and predominant fundamental vibration mode response to wind excitation. MTS Tuned Mass Damper systems are operated essentially as classical Tuned Mass Dampers but are unique in their adaptability, long-term stability, and size. They are designed to minimize energy consumption and offer the structural designer a powerful new means of reducing and controlling dynamic motion.
Although the primary building structure would not depend on the TMD operation for integrity, operation during high wind conditions will help minimize the possibilities of minor non-structural cosmetic damage to building interior components, such as partitions and walls. The TMD system will reduce building motion(induced by moderate and high winds) to approximately one-half of what the building motion would have been without the system operating. If an extremely high gust of wind should impact the building and TMD system can automatically shift its damping coefficient so that the mass does not overstroke. Whenever the system is operating, electronic and mechanical interlock devices ensure that the system is always in damping mode, attempting to reduce building motion, System shut down will occur if an undesirable operating condition should ever develop.
Understanding the Tuned Mass Damper
Understanding the tuned mass damper begins with the basic concept of mechanical vibration: some object is simply moving back and forth in a regular manner. in all cases some physical mass, having inertia, is moving back and forth against a resistance, or restoring force. These two basic ingredients: inertia and restoring force are necessary to all vibrations of common physical objects; in fact,. the presence of both guarantees that vibrations can take place.
One of the simplest possible examples of vibration is a weight, hanging under gravity from a simple coiled spring (Figure 1). Pulled down slightly from the rest position and then released, the weight oscillates up and down. Another example, (Figure 2) is the same weight mounted on the elastic post. Pulled to one side and released, the weight will oscillate back and forth laterally.
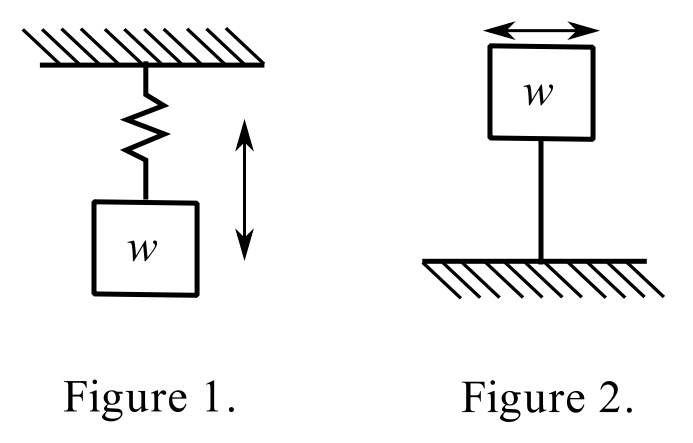
Everything which has both inertia and sporing qualities can thus be expected to exhibit vibration tendencies if once started or excited in some way. Structures such as tall building are exposed to gusty winds and as a result they swap back and forth, or vibrate. Some structures vibrate slowly(i.e., at low frequencies) while others tend to vibrate more rapidly (i.e., at high frequencies).
Example
Consider a multi-story building(Figure 3) having a structural steel frame. Such a building fits all the conditions for vibration. and it will in fact tend to sway very slightly in the wind, moving slowly, requiring perhaps several seconds to accomplish a full swing over and back.
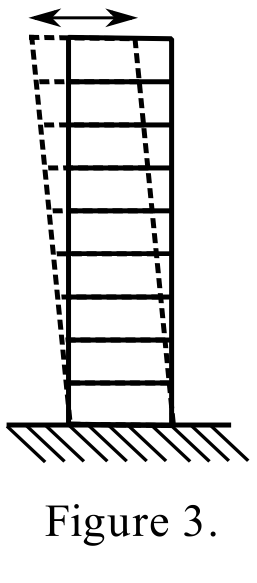
Tall steel freamed building occasionally vibrate enough to disturb their occupants, or at least to draw their attention to the fact that the building is moving or swaying. Actually, buildings oscillate to a much lesser extent then such common structures as aircraft wings and fuselages; yet, because, psychologically, buildings are”suppose” to stand still, occupant objection to building oscillation is often much greater than it is to aircraft vibratory motion. As a result, tuned mass damped systems may be used to lessen building vibration when it occurs.
Other methods may be used to reduce building vibration, but tend to be more costly, or are less certain and reliable. Two possible alternatives are to increase the building mass while maintaining its natural vibration frequency approximately constant, or to increase building damping by adding special energy-absorbing devices or using masonry filler walls.
To achieve the same degree of motion reduction as TMD would require increasing the building weight and lateral stiffness(the structure’s resistance to lateral sway, measured in pounds per inch for example) by a factor of 1 2/3 to as much as 3. The added weight requires heavier structural members and foundations. and the added lateral stiffness requires heavier structure, all of which tend to be very costly. It’s inefficient to invest in very costly large increases in building weight and structure when these increases are unnecessary for safety and are done in order to increase occupant comfort. Methods which reduce building motion by increasing damping are more attractive.
Damping resistance to an vibration is simply any force which tends to dissipate or drain away the energy of that vibration. Damping devices are thus of a type tending to produce friction or bring other energy-absorbing mechanisms into place. For example, the shock absorbers on an automobile dissipate oscillatory energy by hydraulic means. Some tall buildings possess natural damping in the form of masonry cladding walls (the Empire State Building is an example). The inherent friction in masonry construction (or between masonry and steel) is often an effective oscillation damper. Modern steel-and-glass skyscrapers, on the other hand, possess relatively little natural damping.
The tuned mass damper represents an alternative to the damping devices mentioned above. TMD devices have been successfully used to arrest vibrations of power line cables, bridge, and highway-sign structural members, chimneys, tall towers, and antennas, and are used extensively in the automotive and aircraft industry. A TMD does not really act as a damper through energy drainage; instead, it performs in a “reactive” way, temporarily “bouncing” away from the mass it controls. The principles of the tuned mass damper as discussed in the following paragraphs.
Example
Consider the single spring-mass oscillator depicted in Figure 1. The tuned mass damper consists basically of another mass ( the secondary mass) attached by a spring to the first (
) as suggested in Figure 4. The secondary mass is “tuned” to the first in the following sense: The stiffness of spring
and the value of the mass
are adjusted so that the natural vibration frequency of mass
when
is held rigidly still, is the same as that of mass
when
is absent entirely. Clearly, the sense of the word “tuned” in this context is that one vibration frequency(that of the secondary mass alone) is brought into coordination with another frequency (that of the first mass alone).
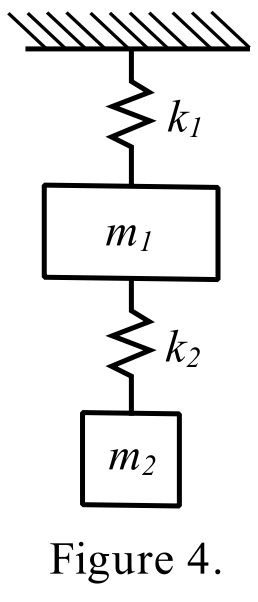
The effect of the presence and tuning of the secondary mass of the TMD is usually dramatic upon the action of the first mass. It tends to greatly reduce or suppress (i.e., “damp”) the vibratory motion of the primary mass. The exact conditions of this action require, and are susceptible to, extensive mathematical analysis.
Suppose a primary mass is excited by some repetitive force that recurs at somewhere near the natural frequency of the primary system. The mass responds by oscillating at large amplitudes, i.e.,”resonating”. Again, suppose a randomly varying force, repetitive but not just occurring at one single frequency, excites the primary mass in a “broad spectrum” of way (i.e., at a mixture of oscillations of many frequencies simultaneously). In either of these cases, the primary mass oscillates manly at its own natural frequency; in the randomly excited case it will also take on random amplitudes.
The action of a tuned secondary mass in either of the above cases is to “take upon itself” the energy of the initial motion of the primary mass and to drastically reduce the response of the latter. This means that any exciting force which acts upon the primary mass must begin over and over again to build up the response of the latter from a low point, since each time that the response of this mass has been even temporarily excited, the TMD reacts against it and suppresses it. As a result there is much less occasion for the primary mass ever to be excited to a condition of excessive displacement, as it might be without the TMD.
The amount of secondary mass needed to accomplish the described effect can be variable, but it has been found that even if it is as small as on percent of the primary mass, it can still produce rather dramatic effects.
When a large, spatially-distributed primary mass consists of a building, like a skyscraper, the entire building may be represented mathematically as a single spring-mass vibrating system, considering not its entire mass as the primary oscillatory element, but only some equivalent(generalized) mass as the necessary element to be dealt with. This is to say that, since part of the building(for example, at the foundation) moves very little, while other parts(say at the top) move much more, the net effective moving mass has a value somewhere between the full mass and zero. This generalized mass also has a location or height coordinate – usually near the top of the building. The magnitude of the generalized mass may then typically range from down to
or even less of the total mass of the building.
The actual amount of generalized mass to be considered depends upon just how the building vibrates – in technical terms. the modes in which it sways. Figure 5 depicts the amount of building sway at maximum travel in typically the first mode. The first mode of tall building sway consists of almost pure “lean” of the building all to one side, then all to the opposite side. Torsional or building twist modes can also occur. In these, the building rotates about an axis more or less coinciding with a straight, vertical line running through the geometric center of each story. Modes higher than first and second can occur in tall buildings but in almost practical cases responses in modes other than the first mode are less important.
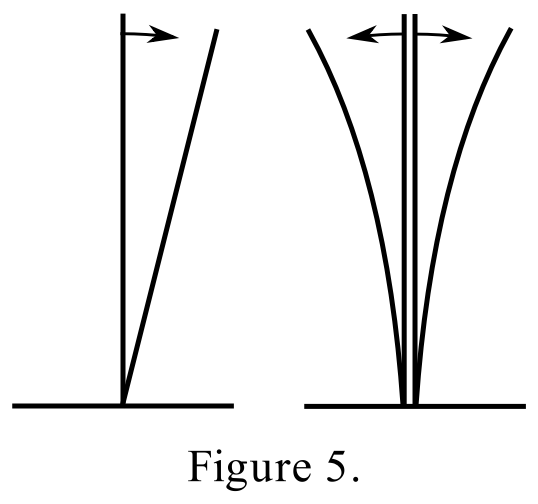
In connection with a tall building, a TMD will be aimed principally at suppressing building sway or twist in “early” modes, say first in sway and first in twist. A possibility, if there is space, is to place inside
, as suggested in Figure 6. This is precisely the kind of situation which exists in a tall building, where a floor may contain the TMD (
).
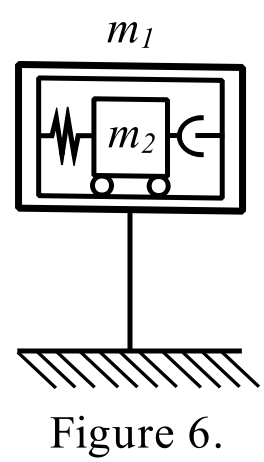
Typically, TMD installations would be a high upper floor (refer to Figure 5) to work against the first swat mode(and twist, if important). The best choice of TMD placement is near the location of the expected highest amplitude of the mode to be suppressed.
The displacement of the secondary mass of the TMD will, when the device is working best, be greater by a factor of three or more depending on TMD design than the displacement of the primary mass. Thus, adequate space and other provisions must be provided for such motion. A second point is that some local damping provided to mass
“broadens” its ability to effectively respond to excitations not precisely at the frequency of tuning. The amount of this local TMD damping also controls the relative displacement of the TMD mass
. The
relative displacement may be reduced by increasing TMD local damping, at the expense of somewhat reduced TMD effectiveness.
The net result of the TMD installation is that the primary mass will respond to wind as if it were damped to an amount at least twice as much as its actual inherent damping. For exmaple, if actual building damping is , a TMD with mass of
the primary (effective) mass can increase total building damping in the first mode to about
while a TMD with mass of
the primary mass can increase total damping in the first mode to over
.
For one of the first TMD systems in a tall office building it was estimated that, to achieve the same reduction of building wind motion, the cost used a TMD system was less than one third of the cost of a conventional approach involving increased building mass and lateral stiffness.
System Description
Principle of Operation:
The MTS Tuned Mass Damper Systems use a moderate force servohydraulic actuator to control the position of a passively resonant spring-mass system. The servoactuator is sized and electronically programmed so that the exact damping and resonant frequency can be electronically set to assure linearity, long term stability, and optimum system characteristics for the particular input motion experienced.
The Tuned Mass Damper systems combine the damper and the servo-hydraulic drive into one servo valve/actuator combination. The system uses substantial flow rates of oil, but requires only a moderate supply pressure minimizing energy consumption while permitting sufficient active actuator forcing capability for accurate operation and adequate cooling.
The passive spring function is derived from two precharged pneumatic cylinders operated in a unique mechanical configuration to achieve force-deflation linearity. Necessary shifts in the passive resonant frequency are accomplished by varying the precharge and hence the spring rate of the mechanism.
A relative displacement program for each Tuned Mass Damper is obtained from a wall mounted accelerometer and an analog computer reference filter. The system is operated in displacement control using the reference filter output as a system command. Damping characteristics of the reference filter are automatically altered at high operation levels so that the mass motion remains within the design stroke limits without affecting the system motion reduction capabilities at low operation levels.
During system operation, the mass is supported by a series of low pressure hydraulically operated pressure-balanced bearing similar to hydrostatic bearings. The bearings operate on a smooth steel surface leveled to tolerance achievable using normal construction techniques.
The TMD systems are fully automated in their operation. The control system continuously monitors the building motion. Whenever the motion approaches perceptible levels, the hydraulic pumps start automatically and the control system moves the mass block as necessary to damp the building motion. Since the motion reduction is on the order of , the TMD system is able to detect when the residual motion has fallen to a level that the TMD is no longer needed. The system then continues to operate for a few minutes before shutting down automatically.
Installations
John Hancock Tower
The first completed fully operation installation is the John Hancock Tower, Boston, Massachusetts. Due to the nature of the floor plan of the building, two TMDs were installed with one being located at each end of the long, narrow building. The TMDs simultaneously work together to reduce the sway in the narrow direction and also in opposition to reduce the twisting of the building. Each mass block weighs tons and is comprised of lead contained in a steel coffer box. In operation, the masses may move up to six feet with an operating cycle of about seven seconds.
Link to a website talking about John Hancock Tower’s tuned mass damper
Citicorp Center
The second fully operational TMD installation is in the crown of the new Citicrop Center, Manhattan(Figure 7). A single pound concrete mass is connected to two orthogonal TMD fixtures to simultaneously damp the Citicorp Tower motion in its two principal axes(figure 8). The TMD was incorporated into the building as a cost saving feature to reduce the amount of structural steel necessary to minimize the peak sway accelerations. The TMD is capable of
inch operating stroke. The operating period is adjustable independently of each axis. The mass block is supported with twelve
inch diameter pressure-balanced bearings operating with a
HP Hydraulic Pump at pressure of
psi. The system is supplied hydraulic power by four
HP pumps which are operated as necessary. The system also incorporates automatic turn-on and turn-off controls.
Tuned Mass Damper of Taipei 101
Enormous pendulum help keep Taiwan’s tallest building from swaying
Inside the Taipei 101 skyscraper in Taiwan is the world’s largest and heaviest tuned mass damper. Essentially acting as a giant pendulum, the enormous steel sphere move slightly back and forth to counter and motion of the building itself. It is an engineering marvel meant to limit the vibrations of the -foot tall building.
The -foot diameter,
-ton steel sphere is suspended by eight cables in the upper stores of the tower and is viable between the 88th and 92nd floors.
As one of the tallest structures in the world located only feet from the major fault line, earthquakes and high winds are a serious threat, In fact, visitors even caught a glimpse of a tuned mass damper in action during the 2008 Sichuan earthquake.
Many skyscrapers contain tuned mass dampers to restrain sway, and as the tops of the tallest buildings can move several feet in the wind a tuned mass damper or similar mechanism is often necessary for maintaining structural integrity. At Taipei 101, the room sized device is capable of moving five feet in any direction thereby reducing sway by to
percent.
Safely comes at a hefty price, however, as the tower’s tuned mass damper costs $ million to build.
Link to Taipei 101′s Wikipedia page
Link to an article about Taipei 101’s tuned mass damper