Biomechanics and Bioengineering of Orthopaedics: Plastics
All plastics are made from specific types of polymers, and the terms polymer and plastic are generally used synonymously (Fig. 8-1). Polymers are created out of monomers. In the example on the screen, our one-unit monomer is ethylene and then when it is polymerized it forms a macromolecule or a polymer which is a chain of the monomers. So, the polymer becomes the component for making the desired plastic.
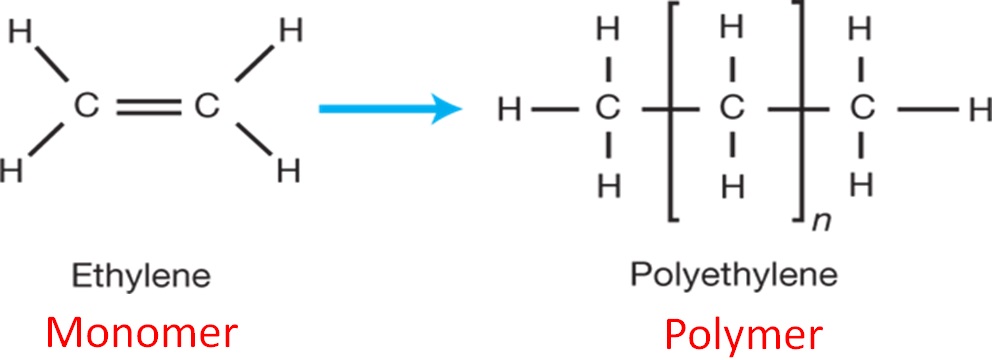
There are 2 main types of plastics, thermoplastics and thermosetting plastics. Thermoplastics can be melted and reshaped whereas thermosetting once heated and cooled are extremely difficult to be reshaped; they retain their form even in extreme heat.
Thermoplastic: Examples are acrylic and polyethylene. They have high impact strength, are lightweight, durable, can be recycled and polished.
Thermosets: Example urea formaldehyde. They give off toxic fumes when heated, are stiff, hard, and brittle, they are scratch resistant, stain resistant and have high tensile strength.
Implantable Plastics
Biomaterials used in the development of orthopedic applications must be exceptionally strong and possess good wear characteristics (Fig. 8-2). For example, individuals participating in sporting activities, experience high loads in their joints that can be as much as 10 times their body weight, and it is estimated that a hip may be exposed to cyclic loading up to one million cycles a year.
High-performance plastics, composite materials and compounds are increasingly being used in the development of a wide range of orthopedic applications. These include spinal fusion cages and plates, artificial discs, acetabular cups, femoral stems and arthroscopic bone anchors and interference screws.
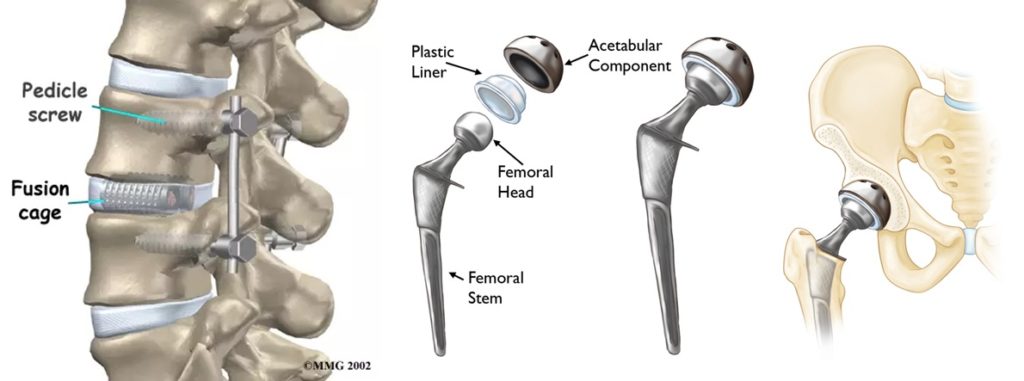
Advantages of plastics as implants
Due to their biocompatibility and high performance, implantable-grade plastics have become a leading biomaterial in the development of orthopedic applications. Since implantable-grade plastics are not metallic, they do not release metal ions into the body, which can trigger allergic reactions in certain patients. Also, because they are non-metallic materials, they resist corrosion, leading to a longer implant life span.
Another advantage is the ability to modify the characteristics of certain implantable-grade plastics. Physical characteristics such as the elastic modulus can be modified to recreate bone modulus. Mechanical properties such as the strength, wear resistance and impact performance of polymers and composites can be comparable to metals and offer additional benefits.
Implantable plastics also eliminate artifacts during post operative examination by traditional techniques such as X-ray, CT and MRI technology.
Plastics are made from polymers which are also less dense than metals and have lower thermal conductivity. They also provide better color aesthetics especially in areas close to the translucent skin surface. In addition, polymers present the ability to be surface modified with such coatings as hydroxyapatite or titanium, to aid in secondary fixation or with chemical species as with bone morphogenic proteins (BMPs).
Implantable Plastics: UHMWPE
UHMWPE, ultra-high molecular weight polyethylene had been one of the common polymers used in the development of implantable orthopedic applications (Fig. 8-3). UHMWPE is biocompatible, has excellent impact strength, a low coefficient of friction and good fatigue resistance. For these reasons, it has been used for many decades to manufacture orthopedic applications used in the hip, knee and other joints. Though the material has proven successful in these areas, it is not used in the development of load-bearing applications, such as spinal cages, due to its relatively poor mechanical strength compared to other polymer alternatives. While UHMWPE is considered to have a low relative wear rate, there have been concerns about tissue reaction to the wear particles and resulting implant loosening.
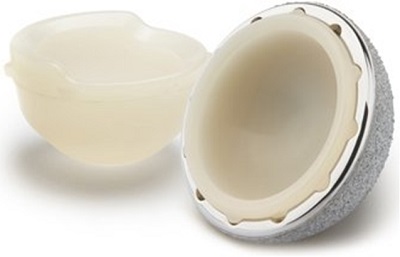
Implantable Plastics: Polyetheretherketones (PEEK)
Device manufacturers today, are exploring the use of implantable plastics that possess high performance and customized properties, as they allow for greater design freedom and ultimately lead to improved applications. The most widely used long-term implantable plastics include polyetheretherketones (PEEK).
Implantable-grade PEEK (Fig. 8-4) was introduced because of its mechanical properties, which include good wear and impact resistance, long-term biocompatibility and biostability, inherent lubricity and high compression strength. PEEK can also be modified to improve its mechanical properties by adding carbon-fibers to the polymer matrix.
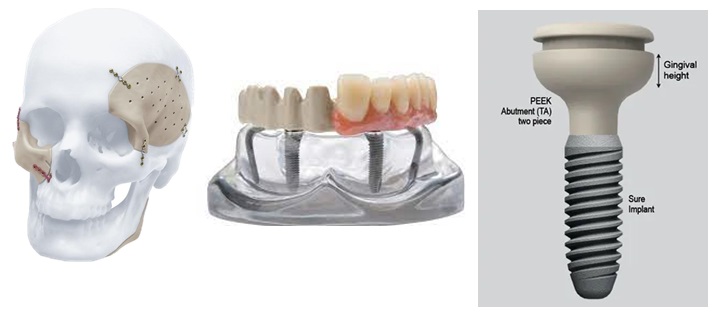
Furthermore, PEEK has other useful engineering properties such as thermal stability which is very important with plastics. Other properties include chemical resistance: PEEK is insoluble in most polymeric solvents and also does not undergo hydrolysis, even at high temperatures. This, coupled with its relative inertness to chemical reactions, means that it is perfect for biomedical applications where constant sterilization at high temperatures is important.
PEEKs are also combustion resistant, have a high melting point and offer good electrical insulation. All these properties are retained at temperatures close to their melting points due to the crystalline structure of these polymers and that makes them very unique.
Implantable Plastics: Bioabsorbables
Bioabsorbables include polylactic acid (PLA), polyglycolic acid (PGA) and their copolymers (Fig. 8-5).
Bio-absorbables are engineered to dissolve inside the body via hydrolysis and enzymatic activity and have a range of mechanical and physical properties, which can be engineered appropriately to suit particular applications. Their degradation characteristics depend on several parameters, including their molecular structure, crystallinity and copolymer ratio.
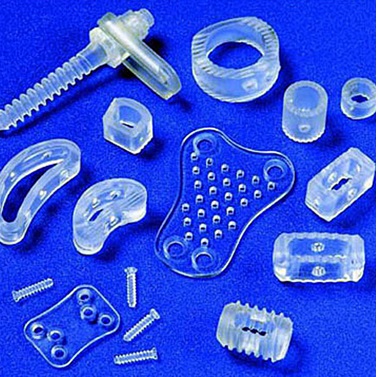
Bioabsorbables are designed to dissolve in the body and by so doing, they gradually transfer the load to the bone or soft tissue as it heals. This eliminates a second surgery that may otherwise be needed to remove metallic implants. PLA, PGA and their compounds are the most common commercialized bioabsorbable polymers. The rate of degradation of these implants can be altered based on the material composition and is set to match the implant dissolution with the healing rate.
These polymers are used in orthopedics primarily for sutures, bone pins and screws. However, they do not have the mechanical properties required to be used in the development of load-bearing applications.